The Commerce Department issued a report listing best practices ports should consider adopting to optimize efficiency and improve competitiveness in the face of capacity constraints associated with larger cargo ships and ocean carrier consolidation.
The Commerce Department last month issued a report listing best practices ports should consider adopting to optimize efficiency and improve competitiveness in the face of capacity constraints associated with larger cargo vessels and consolidation in the container shipping industry.
The findings weren’t especially newsworthy, since several ports have implemented well-publicized programs to engage stakeholders in a whole-of-supply chain approach to speed cargo flows, but the report does serve a purpose. It gathers best practices in one place and gives them more weight with government backing.
Recommendations for port authorities include:
• Establishing working groups, with broad stakeholder participation, that serve as forums for productive communication and collaboration;
• Using customized information sharing technologies that improve operational efficiency and cargo status data flow between a port, terminal operators and others in the transportation chain;
• Expanding public-private investment to improve port operations, infrastructure and IT;
• Implementing operational improvements that facilitate container chassis availability (e.g. chassis pools), allow more efficient planning and scheduling, improve terminal use, and reduce truck turnaround times;
• Setting performance indicators voluntarily agreed to by community members, such as for gate turns, and then measuring efficiency against those benchmarks;
• And working with local educational institutions to improve existing port workforce skills, retention rates and recruitment.
The department’s approach is to share the best practices so that port communities can voluntarily adopt comparable measures that meet their unique circumstances.
“Our ports need new ways to achieve efficiencies that speed their operations and the flow of their stakeholders’ cargo. It has become crucial for ports to have an open dialogue with the full range of their stakeholders to address challenges that inhibit operational efficiencies,” then-Secretary of Commerce Penny Pritzker said in the report’s preamble.
Ports are complex ecosystems, supporting interconnected supply chain activities of multiple actors, including railroads, motor carriers, longshoremen, terminal operators, warehouses, shippers, and chassis suppliers. Anything that impacts one part of the supply chain can cause disruption at the port, and port disruptions can have upstream and downstream effects on cargo movement. Ports perceived as inefficient can lose shipper and carrier customers to alternative locations in the United States, or other countries in the case of exports. The best practices are intended to help U.S. ports meet customer expectations.
The report was based on the work of a federal advisory committee on supply chain competitiveness that meets quarterly to provide industry input to Commerce Department policymakers, as well as lessons learned from a series of listening sessions and a supply chain conference in Southern California. Members of the advisory panel include Rick Gabrielson, vice president of transportation at Lowe’s; Dean Wise, vice president of network strategy at BNSF Railway; Gene Seroka, executive director of the Port of Los Angeles; and Leslie Blakey, president of the Coalition for America’s Gateways and Trade Corridors.
The impetus for developing the recommendations stems from systematic performance failures at major container ports during the past four years as the maritime section of the supply chain struggled to adjust to new industry dynamics presented by the introduction of ultra-large vessels and the expansion of ocean carrier alliances.
Vessel sharing alliances have helped the struggling liner industry reduce costs by allowing carriers to consolidate cargo on partner ships to maximize capacity utilization. But the practice has resulted in massive surges of cargo at a single terminal, rather than being spread out on several vessels across a port complex, making it difficult for terminals, railroads and motor carriers to find enough labor, equipment, and storage space to handle the containers in an efficient manner.
The situation reached a breaking point two years ago, when negotiations over a new labor contract for dockworkers at West Coast ports hit a wall, resulting in a work slowdown that virtually froze cargo movement in and out of ports for several weeks. Many importers and exporters suffered damage from lost sales when they were unable to meet delivery commitments, spoilage of perishable cargo, and extra transportation costs associated with emergency re-routing of cargo to other ports and modes.
In the past year, the ocean carrier industry has undergone rapid consolidation through a series of mergers, acquisitions and bankruptcies. And all that movement has caused carriers to restructure and consolidate their alliances as well.
Many of the ideas in the report are already being implemented at U.S. ports, but advisory committee members have said that businesses are more likely to collaborate in joint working groups when the suggestion comes from the federal government.
The ports of Los Angeles and Long Beach, for example, already have a pilot “free-flow” program under which containers for certain consignees or destinations are grouped and lifted onto trucks from the top of a pile, in contrast to the traditional, more time-consuming method of culling through stacks to dig out an assigned load for each trucker. The two ports, as well as others, have also convened working groups that meet on a regular basis to address operational pinch points and discuss long-term planning initiatives.
Commentary: Feds offer tips on port productivity
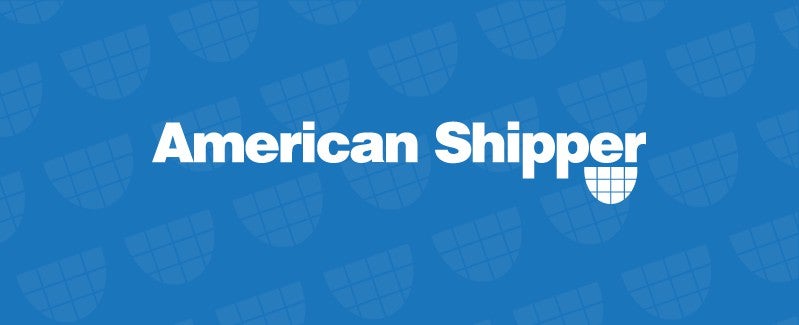
Eric Kulisch is Trade and Transportation Editor of American Shipper. He can be reached by email at ekulisch@shippers.com.