Union official worries technology could cost longshoremen jobs, but former executive says pride in work would provide security.
Collective bargaining between West Coast dock workers and waterfront employers for a new contract has revolved around issues such as wages, health benefits, pensions and retaining jurisdiction over chassis maintenance, but many maritime industry professionals suspect that another unspoken sticking point has been the degree to which container terminals automate cranes, entry and exit gates, cargo handling equipment and other functions.
During the last contract that expired at the end of June, the International Longshore and Warehouse Union agreed to allow technology at marine facilities as long as the parameters of each deployment were negotiated on a case by case basis.
As terminals become overwhelmed by concentrated growth in volumes, many experts say mechanization and computerization are needed more than ever to load and unload bigger vessels, shuttle boxes to and from the storage yard, stack containers, lift them on and off truck chassis, and process trucks through the gates.
Two terminals in Southern California – OOCL’s Middle Harbor facility at the Port of Long Beach and the TraPac Terminal at the Port of Los Angeles – are being upgraded to include automated rail gantry cranes and other technology that will make them among the most modern port facilities in North America.
The ILWU’s formal position on automation doesn’t necessarily mean that rank-and-file longshoremen or their union bosses are comfortable with automation just yet.
An ILWU official at a port productivity conference in December provided a window into the union’s mindset towards technology and its perceived threat to members’ jobs.
“The word automation scares the hell out of me,” Jeff Smith, a member of the ILWU’s Legislative Committee from Local 8 in Portland, Ore., remarked from the audience during a panel on port labor at the Journal of Commerce-hosted event in Newark, N.J.
He acknowledged difficulty adapting to technology, saying “it was hard for me to use an iPhone. It was hard for me to use a computer when it came out.”
Several terminals have centralized gate operations instead of manning booths in each truck lane by using cameras, speakers, card readers and radio frequency identification systems to verify the truck, driver and dispatch assignment. A fewer number of workers can process all the trucks from a remote office.
Some container lines carry out ship planning and customer service from remote locations such as Phoenix, Salt Lake City or Denver.
“Well, that scares us because if you can do that with a computer who knows that we’re not going to be loading ships from Billings, Montana, or Salt Lake City?” Smith said. “That scares the hell out of labor. And that’s why the resistance is there when the negotiations go on because we have to secure our future.”
He even expressed fear that welding jobs on the docks might be eliminated.
Anthony Scioscia, a former head of APM Terminals North America who now heads his own eponymous port management advisory firm, assured Smith that mechanics who repair equipment will not be replaced, but noted that new mechanical equipment and information technology “requires a different skill set, not only to operate the systems, but to repair them. So, the rank-and-file is going to have to be brought into the industry that has those skills and abilities.”
At a press conference on Wednesday about the latest contract offer, Jim McKenna, the president and chief executive officer of the Pacific Maritime Association said, “Automation has not been part of the negotiations at all. Automation was in 2008 and hasn’t been a part of these discussions even a little bit.”
Asked about training of workers on automatically controlled equipment, McKenna responded, “We always talks about training, but it is training in general, than specific. Automation has not been front and center in these negotiations at all.”
Automation is not unique to the port industry. Workers in the manufacturing sector, especially in Europe, tend to get retrained with better skills and their compensation eventually goes up, Walter Kemmsies, chief economist at port engineering firm Moffat & Nichol, said during a presentation at the Transportation Research Board’s annual conference in Washington last month.
“Whenever the volumes increase and we use machines for something it’s because we need labor to be doing something else. So there will be alternative jobs,” Kemmsies said. “Whether employment growth will be as great as during the early parts of containerization – probably not. But, then again, containerization was a phenomenon changing the structure of an industry” that has now matured.
Workers tend to benefit in the end, “It’s just the short run that’s scary and unstable,” he added.
Terminals would face less pressure to automate if unions did a better job policing their members to make sure nobody slacked off and undermined productivity, James Devine, who retired last year as the CEO of New York Container Terminal, said.
The ILWU and the International Longshoremen’s Association on the East Coast have failed to discipline longshoremen who short-time employers, he argued.
“In the new contracts, the ILA and the ILWU have to step up to the table and take an active role in making sure the workforce that they sponsor is properly motivated with positive, and when appropriate, negative measures to make sure that you don’t have the one crane operator who does 35 to 40 moves an hour and then other crane operators get up there and deliberately do 22 moves an hour” to stick it to management, Devine said from his perch in the audience. “And when you call them to task for it, the union puts their arms around them and protects them,” excusing the action as falling within a “sustaining pace,” he said.
Devine is now a senior associate with Mercator International, a boutique management consulting firm focused on logistics and infrastructure.
In an aside to a reporter during a break, Devine added, “It’s incumbent on the ILA and the ILWU leadership to bring that home to them. They are well paid. They need to come to the terminal and do their job.
“That’s the problem. Some percent of the workforce tries to get over and do as little as they possibly can. And that’s what drives the automation for some people. Get rid of this guy because he’s sitting at his desk playing a word game and he’s not attending to the gate. If the guy was doing his gate job, you wouldn’t have to spend the money [on technology] and he would have protected his job.”
Devine couched his comments by saying that he is a firm believer that labor is a critical component of ports, that it needs to be at the negotiating table and involved in creating value-added positions. He stressed that terminal operators’ first responsibility is to ensure the safety of workers and that they should show them respect by taking care of details such as having clean, fully stocked restrooms and making sure windshield wipers on vehicles work well.
Companies should sit down with their unions, be transparent about their goals, follow the contract protocols regarding automation and do the proper bargaining over how many people will be impacted by technology, Scioscia recommended.
“If you do that and you are honest and sincere about it, I think you can get it done,” he said.
Automated terminals remain deep-seated fear for ILWU
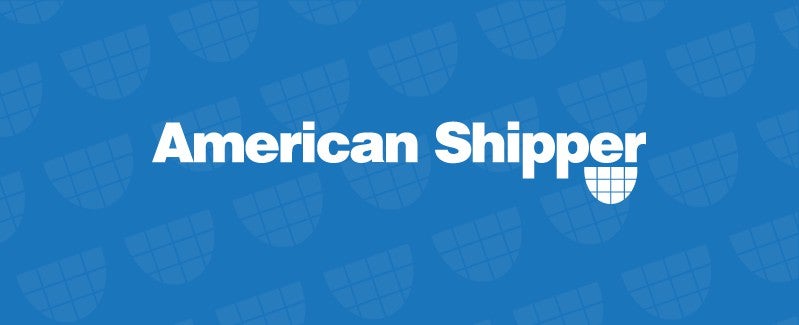