Agriculture shippers ask Senate for help with overcoming “significant challenges” in ocean shipping that could hurt the American economy.
A top logistics official from Tyson Foods told Capitol Hill lawmakers on Wednesday that implementing the International Maritime Organization’s Safety of Life at Sea (SOLAS) Convention’s July 1 requirement to verify the weights of containers before they’re loaded onto ships is “by far the most urgent issue facing shippers today.”
In written testimony, Perry M. Bourne, director of international transportation and rail operations at Tyson, further explained to members of the Senate Commerce Committee’s subcommittee on surface transportation and merchant marine infrastructure, safety and security, that providing carriers with the verified gross mass (VGM) of containers — the combined weight of the box and its contents — adds to the “significant challenges” faced by agricultural shippers, potentially disrupting U.S. exports and harming the American economy.
Bourne, who also testified on behalf of the Agriculture Transportation Coalition (AgTC), said Tyson and other AgTC members “have serious concerns with being responsible for verifying the weight of shipping containers that we do not own, lease or operate.”
AgTC has proposed that shippers be only required to provide the weight of their cargo and carriers should provide the weight on their containers, and noted this is acceptable to the U.S. Coast Guard.
However, Bourne said ocean carriers, as represented by the World Shipping Council (WSC) and Ocean Carrier Equipment Management Association (OCEMA), are insisting that AgTC’s suggestion is not acceptable.
“They contend that the shipper must be responsible for verifying the weight of the containers owned or leased by their own members. I will not speculate on why the carriers have adopted such an inflexible position. But we can certainly predict the possible impacts at the ports if the carriers do not change their position and agree to a reasonable resolution of this issue,” he said.
Bourne said “approximately 75-85 percent of Tyson Foods’ protein products bound for export markets are shipped to the U.S. ports by domestic rail or truck. These products are then trans-loaded from the domestic conveyance to the ocean carrier’s container.
“Tyson’s plants and freezer facilities are located anywhere between 1,100 and 2,200 miles from the U.S. West Coast ports. When we book an export load for shipping, although the ocean carrier has the weight information of all their container assets in its data base, the actual weight of the specific container assigned to Tyson’s booking is not known at the time of loading,” he explained.
“As a logistics professional, I appreciate and understand this fact. However, if the rules are going to be changed that require shippers to find a way of obtaining the specific weight information on a container, we will have to develop some method of obtaining this information in a timely manner from the carrier or from the trans-loader,” he added. “The alternative is trying to obtain the actual container weight at the port, which risks missed sailings.”
For example, Bourne noted “Tyson moves between 70-80 loads of chilled meat on a weekly basis. These loads are shipped Wednesday through Friday from our facilities and arrive by truck at the West Coast ports on Sunday and Monday. The cut-offs for delivery to the ocean carriers are Monday for a Tuesday sailing.”
He warned if the SOLAS approach favored by the carriers is adopted, and Tyson is unable to obtain the specific container weight until the time of trans-loading, “under the carriers’ own rules any cargo trans-loaded late would have to be delayed for the following week’s sailing and we would be required to air freight the cargo or forced to convert a chilled fresh product to a frozen product. All of these alternatives mean lost sales, and potential lost market share, in valuable export markets such as Asia.”
He asked for the Senate committee’s support “in insisting on a solution to SOLAS that is both compliant and supportive of U.S. export growth.”
In his testimony, Bourne also highlighted continued congestion at West Coast ports.
“I have food products to move,” he said. “Some of it is very time sensitive. If we don’t deliver what our customers want on time, we develop a reputation, both as suppliers and as a source country, of being unreliable. Our customers can and do buy similar protein products from Australia, Brazil and the European Union countries. The United States is not the only game in town.”
Bourne applauded efforts by the Federal Maritime Commission to bring together industry working groups of stakeholders in an effort to identify what is “causing the persistent delays at the U.S. ports and to propose meaningful solutions that will make our ports the most productive and efficient in the world.”
At a Wednesday FMC meeting, a few blocks away from Capitol Hill, Commissioner Rebecca Dye said on May 3 a group 36 leaders in the ocean cargo logistics industry, who are part of the FMC’s Supply Chain Innovation Team Initiative, will meet for two days.
The FMC said “three small multi-industry innovation teams will begin discussion on supply chain challenges by identifying actionable process improvements.” Industry experts who are expected to participate in the agency’s initiative, will come from ports, terminal operators, large shippers, ocean transportation intermediaries, port labor, railroads, truckers, and chassis providers. Academic advisors will include John’s Hopkins University’s Applied Physics Lab, the Transportation Institute at the University of Denver, the New York Shipping Exchange, Strategic Mobility 21, MIT’s Center for Transportation and Logistics, and others, the agency said.
“The goal of the 36 participants in our three innovation teams will be to develop actionable commercial improvements, and move beyond discussion to action,” Dye said.
Bourne added “From our perspective, many of the issues that have beset the U.S. West Coast ports in particular have arisen from the consolidation of carriers into these foreign-flagged mega-alliances,” which he said can create added congestion.
“Increased congestion at ports, which is already a recurring problem, can mean delays, added costs and even missed sailings. This hampers U.S. export growth. We would like to see a more thorough review of these foreign carrier alliances by the FMC to ensure that their actions do not result in a logistics network within the ports that adds more truck trips and congestion to an already overloaded port infrastructure,” Bourne said.
“From our perspective, this is exactly what is happening. In recent years, we have already seen fewer ships and sailings with the advent of supersized vessels of up to 20,000 TEUs and reduced infrastructure as the carriers have eliminated their own of chassis operations. Now the addition of the alliances and shared sailings has added even more to the shore-side costs of shippers trying to deliver cargo to the ships,” he added.
Bourne made his comments on the same day that CMA CGM, COSCO Container Lines, Evergreen Line and Orient Overseas Container Line (OOCL) announced they had signed a memorandum of understanding to form a new vessel sharing agreement they are calling the OCEAN Alliance.
Food producer says SOLAS rule ‘most urgent issue’ for shippers
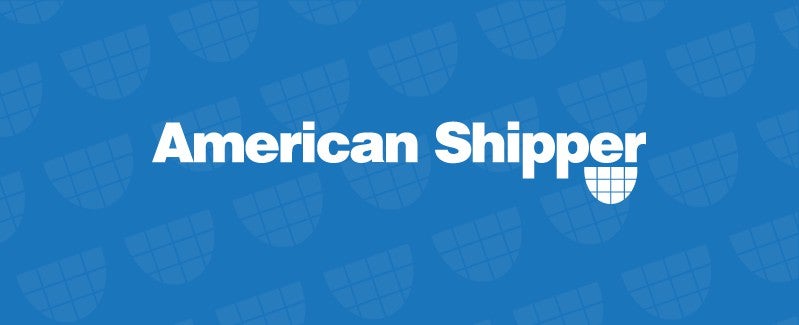