Congestion, delays and bad weather created “a perfect storm” and led to $5.6 million net loss.
Fresh Del Monte Produce said its transportation operations were hit with both a figurative and literal “perfect storm” in the second quarter.
While net sales nudged up slightly to $1.27 billion in the three months ending June 29 from $1.15 billion in the same 2017 period, the company reported a net loss of $5.6 million in the second quarter of this year compared with a profit of $69.8 million in the second quarter of 2017, putting much of the blame on higher transportation and logistics costs.
“Uncontrollable factors led by congestion, delays and inclement weather at our loading ports in Central America, substantially lower banana selling prices in Europe, an oversupply of pineapples in North America, continued tightening of the transportation market and higher commodity costs adversely affected our overall performance,” said Mohammad Abu-Ghazaleh, chairman and chief executive officer of the Coral Gables, Fla.-based company.
Elaborating during an investor phone call this week, he said inland transportation and logistics costs in North America were $13.4 million higher year-over-year, “largely due to trucker shortages, new regulations on drivers, higher fuel cost and port delays.”
“Bunker fuel cost per ton increased 30 percent and represented 2 percent of our total cost of sales,” said Richard Contreras, chief financial officer. “Total ocean freight cost during the quarter, which includes bunker fuel, third-party charters and fleet operating cost, increased 3 percent and represented 7 percent of our total cost of sales.”
Abu-Ghazaleh said the situation was “a perfect storm, really that was not expected at all.”
“Unfortunately, everything turned around beyond our control,” he said. “We had such bad weather, with very poor port management in Costa Rica and Guatemala.”
“Both of these countries never had such congestion and bad weather like we experienced in the last quarter,” he said. “Ships had to wait two to four days in order to be able to load.
“Once we lose that slot, the ripple effect is tremendous, because we lose our kind of schedules coming into the discharge ports. … I can give you 10 different kinds of consequences of this. We missed delivery to our customers. We have to ship fruit from other ports to be able to sustain our customer needs, which means off-port charges, which would translate in millions of dollars, as well as the quality was also affected by delays at the port.”
Even in the United States the company had to contend with bad weather — snow and rain — at East Coast ports from March through May, he said.
In its annual report filed with the Securities and Exchange Commission, Fresh Del Monte said, “Because logistics costs are also our largest expense other than our cost of products, we devote substantial resources to optimizing our logistic network.”
At the end of last year, it transported fresh produce using a fleet of 11 owned and seven chartered refrigerated ships and operated four port facilities in the United States. It also operated a fleet of 6,000 refrigerated containers — 2 percent owned and 98 percent leased.
The company said during December 2017 and the first six months of 2018, it entered into definitive agreements for the building of six new refrigerated container ships for approximately $173.2 million. It said the shipbuilding program will replace its entire U.S. East Coast fleet of vessels.
Fresh Delmonte has port facilities in Gloucester, N.J. on the Delaware River, Port Manatee, Fla., Galveston, Tex., and Port Hueneme, Calif.
While the Del Monte brand was established in 1892, the fresh food business was separated from the canned business in 1989.
Fresh Del Monte: Transportation costs spoiled Q2
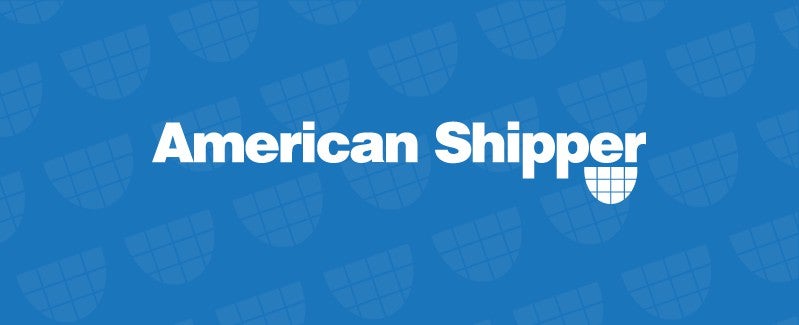