Shippers voiced concerns about bigger containerships and larger carrier alliances last week during a panel discussion at the South Carolina International Trade Conference.
Pointing to the proposed P3 alliance of Maersk, Mediterranean Shipping Co., and CMA CGM, the expansion of G6 alliance to include not only the Asia-Europe trade, but also services between Asia and the U.S. East Coast, and possible expansion of the CKYH alliance, Klaus Schnede, manager of marine and air facilities procurement at Eastman Chemical, said “it is very concerning to us as an exporter that there may be less choices in the future.”
Eastman exports about 40,000 TEUs annually.
He recounted when the G6 began serving the East Coast, transit time from Savannah to Japan on one string doubled. He said, however, his company was able to switch to another G6 carrier and obtained a better transit time.
Schnede said larger ships and alliances could have positive aspects as there may be more space for cargo, more port coverage, and additional weekly services. He also said while rates may initially go up, in the long run, shippers may benefit from lower freight rates.
But he questioned how carriers will be able to differentiate themselves when their cargo is all riding on the same ships, saying that customer services- for example, the ability to get a live person on the phone – was not good at some carriers.
He said carriers can differentiate themselves by having better equipment and more space.
Schnede said as alliances grow, shippers will have to pay more attention to what vessels are actually carrying their cargo. With multiple carriers sharing space on the same ship, shippers run the risk of placing too much cargo on a single vessel, which he noted could be risky in the event of an accident.
Frank Baragona, president of CMA CGM (America), told the conference the P3 alliance will create “enormous synergies” and reduce costs, and said the three carriers have “a very coherent plan for vessel integrity and on-time performance.”
He said CMA CGM will be able to add new lanes and markets it is not in today, and provide capacity and space. Instead of shippers putting all their eggs in one basket, he said “we are going to spread that basket out.”
Eric Sherman, divisional vice president of imports at Family Dollar, said his company was a long-time user of ports in the Southeast, and expressed concern that as ship sizes grow, problems his company has seen in the Los Angeles/Long Beach area could develop in the Southeast.
He said several years ago his company began to move cargo through L.A./Long Beach and opened a West Coast transload facility.
“I can’t tell you how many times I’ve thought about it and said ‘why did I do this?’ The aggravation and stress on the West Coast, Southern California in particular, the costs and the challenges, sometime I wonder. Then I look back at the South Atlantic and relax a little bit,” Sherman explained.
He said as ships are getting bigger, vessels are taking longer to unload. He said drivers are having to spend more time at terminals to pick up cargo.
Speaking about the ports of Los Angeles and Long Beach, he said, “From what I hear from my team members out West, it’s a nightmare right now.” He said because of terminal congestion at night and the PierPass program, Family Dollar is spending more to pick up cargo during the day and the appointment system for truckers to collect cargo “is a disaster.”
Under the PierPass program truckers must pay a traffic mitigation fee when picking up cargo between 3 a.m. and 6 p.m.
The PierPass Website said among “frequent callers” – that is, trucks that make one or more moves per weekday – in July 2013, 14 percent made five moves, 20 percent made four moves, 28 percent made three moves, 22 percent made two moves, and 16 percent made one move.
Paul Morin, head of U.S. transportation and global logistics at Adidas Group, said his company also has a cross-dock facility in Southern California and is examining whether it’s the right place to be. He said his company’s PierPass costs “were in the high six figures” and it’s a “cost we are trying to drive out of our supply chain.”
Sherman also said at one terminal he visited there seemed to be more chassis in maintenance and repair than in the available pool.
“I know some importers are even building in extended lead times into their models so that whatever the carriers are projecting as transit times they are adding another 4-6 days into theirs, just to get access to the equipment,” he said.
In contrast, Sherman said Southeast ports have quick turn-times and are service-oriented, and chassis pools are more flexible.
But he’s concerned about the future as bigger ships come to the East Coast, noting the long time needed to complete harbor-deepening projects and requirements to improve landside infrastructure.
He noted because of congestion in the Port of New York and New Jersey this summer, some carriers diverted cargo to Norfolk, Va., and he said the two ports are “disasters” as a result.
“If basic shifts in volume like that are causing major production issues in terminals today, how are we going to get there tomorrow?” Sherman said.
“We have a great thing going down here,” he said. “We need to continue to grow this area.”
Adidas’s Morin said shifts in arrival times of vessels can cause big problems.
Estimated time arrivals (ETAs), he said, no longer stands for estimated time of arrival, but exact time of arrival.
“Oftentimes shifting ETAs cause havoc within our supply chain, within our ERP system in terms of when product is available for customers. We are under constant pressure to meet the ETAs that we have agreed upon with carriers,” Morin said.
“Speed-to-market products, reacting to customer demand, improvement in inventory turns, it is all pressure that impacts us on a daily basis,” he added.
Morin said when contracting with carriers, his firm looks for not just the shortest transit time, but the most reliable, because if product does not arrive on time, there is a ripple effect.
He also expressed concern about the time that “megaships” take to discharge containers.
“We are given an ETA for a Sunday arrival, but we can’t get the box until sometimes Wednesday or Thursday, it is very frustrating,” Morin said.
Internally, he said it’s hard to explain to other departments of a company, such as purchasing or customer service, when they see a ship has arrived on Sunday but it may be a week to move container 60-70 miles.
He said his company is building an extra four to seven days into transit time from Asia to the West Coast, in part because of slow steaming, but more because of the time vessels take to offload and efforts to avoid incurring PierPass expenses.
While some carriers can get access to their products more quickly by asking for it to be loaded in a “hot hatch,” Morin noted because of fast-moving changes in consumer behavior, it is sometimes difficult to know how popular a product is going to be when cargo is loaded on a ship.
Adidas has a major warehouse in Spartanburg, about 15 miles from the inland port that the South Carolina Ports Authority is building in Greer. Morin said about half the company’s cargo comes through Charleton so the inland terminal potentially offers a positive benefit to his company “if the schedule is realized and we can get access to the boxes.” – Chris Dupin
Shippers voice concerns over mega-ships, mega-alliances
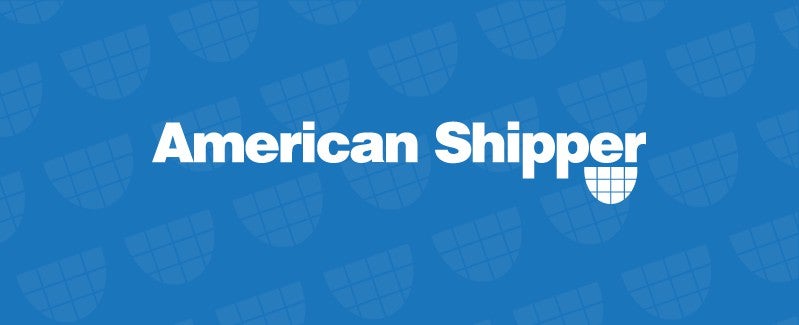