FreightWaves is providing a forum – Market Voices – for a number of market experts.
Dean Croke grew up in a family trucking business and spent years as an over-the-road truck driver and manager of large trucking fleets. Dean has been able to combine his practical experience with extensive knowledge of human physiology, logistics and supply chain management.
Over the last decade, Las Vegas has changed from “buffets and bingo” to a sports fan’s heaven. In the process, the city is in the process of “recession-proofing” itself and because of that is in the midst of a construction boom. This boom has created significant demand for flatbed carriers that haul millions of tons of freight into the city each month.
There are many things that catch your eye in Las Vegas, but at the recent Truckload Carriers Association convention, it was apparent that the city is going through a construction boom. Tower cranes dominate the skyline and flatbeds unloading steel and building products are only surpassed by the large volume of belly-dumpers moving type two dirt or “haul-off,” as it’s locally known, from any one of seven large construction projects underway.
According to construction industry experts, these major projects in Las Vegas total $10 billion and are expected to open by the end of 2020, provided project-build timelines stay on track. These mega-projects include the new $1.9 billion Oakland (soon to be Las Vegas) Raiders NFL Stadium, which is planned to be operational for the 2020 football season. The stadium will also be the home stadium of the University of Nevada, Las Vegas Rebels football team. Other huge projects are the 87-acre $7 billion Resort World Casino, and the $1 billion Las Vegas Convention Center (LVCC) expansion. As a measure of how much Las Vegas has grown as a convention destination, the LVCC is ranked as the number one trade show destination in North America with 400 conventions already booked in 2025.
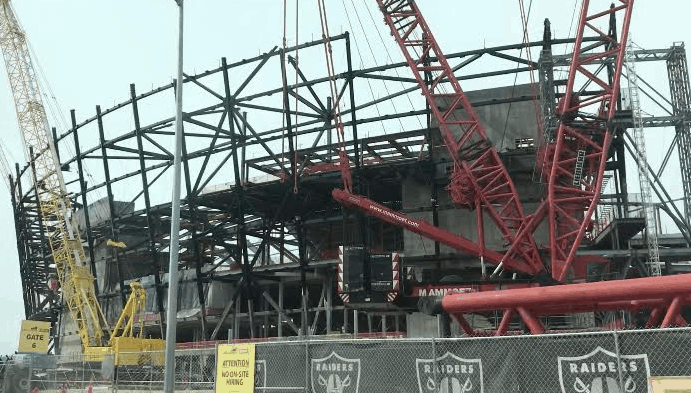
A sports hot-spot
According to leading Las Vegas realtor Bill Margita, “Las Vegas is set to see the largest amount of commercial development in its 100-year history…in just two years.” Margita said, “Las Vegas was hit so hard by the recession we had to figure out how to make ourselves recession-proof, and that’s why today you see so much commercial development in industries other than gaming. We studied all of the cities around the world to find out what made them recession-proof, and it came down to one thing – sports medicine.”
It’s no accident that sports is now a big part of the Las Vegas economy. In addition to the previously mentioned Las Vegas Raiders, the list of professional sports teams making their way to Las Vegas includes the Women’s National Basketball Association Las Vegas Aces team (relocating from San Antonio), the National Hockey League’s Golden Knights ice hockey team, the United Soccer League Las Vegas Lights Football Club, and the Las Vegas 51s, a Triple-A minor-league baseball team affiliated with the New York Mets. Las Vegas is also home to Ultimate Fighting Championship (UFC), the largest mixed martial arts promotion company in the world.
All these teams (as well as amateur athletes) need hospitals and sports medicine facilities, which brings us back to the current construction boom driving demand for flatbed trucking. The growth of sports and sports medicine also serves another purpose, and that’s to provide improved healthcare to aging baby-boomers seeking a warmer climate and a healthier lifestyle. According to Margita, “sports help cities thrive, and because baby-boomers are the wealthiest generation in history and are looking to extend their productive lives as long as possible in retirement, the city realized that the best way to make Las Vegas recession-proof was to build a city around the people who live there, not just those who visit to spend money and have fun.” And if you’re wondering where the money comes from, take a look at your hotel room bill next time you’re in town. Even though the room rate may appear low, the added “resort tax” of $25 is how funds are generated for many of the current construction projects.
Steel jigsaw puzzles
All of the commercial construction projects currently underway, and the associated infrastructure to support them, require a substantial amount of building materials – including structural steel. Most of that steel has to be transported long distances from specialty manufacturers such as Merrill Steel, headquartered in Scholfield, Wisconsin.
Merrill Steel is supplying roughly one-third of the steel for the new Las Vegas Stadium; the 10,000-ton order is the largest steel order the company has ever fulfilled. To translate that into truckload demand, it’s the equivalent of 400 flatbed loads from the company’s Springfield, Missouri factory to Las Vegas, some 1,400 miles away or almost three days by truck. It’s expected that by the time the new stadium is completed, around 1,200 flatbed loads of steel will have been delivered to just that one construction site. By the time the Las Vegas construction puzzle is complete towards the end of 2020, industry experts estimate around 20,000 loads of steel will have been delivered by flatbed truck.

It’s generally accepted that flatbeds are a good indicator of economic health. Flatbeds haul materials needed for the building and construction sectors, and judging by the number of flatbeds in Las Vegas, the economy is booming. At the famous Wild Wild West Travel Plaza in Las Vegas, there are, on any given day, an average of 300 pre-loaded flatbed trailers being staged awaiting delivery to the new domed stadium that is just a mile down the road. No two trailers are loaded with the same steel, as each load is designed to fit perfectly in sequence into the steel jigsaw puzzle they are building.
Orders follow price
According to Donald Broughton, managing partner and principal of Broughton Capital and chief market strategist of FreightWaves, “demand in one city doesn’t mean business is booming everywhere else though.” He created proprietary monthly indices based on DAT data that measure activity in the spot and contract markets based on rate and load availability. The DAT Freight Barometers are indexed to 50 and indicate whether or not there is heightened market activity on a national level for each of the three trailer types tracked (flatbed, dry van and refrigerated trailer). In a booming economy, the higher the number the more activity there is, which indicates price and/or volume are increasing.
As of mid-March, the latest numbers place the flatbed barometer at 53.24, but to put this into context, Broughton said, “2018 was such an extraordinary year, as you can see by the data in FreightWaves’ SONAR. The flatbed barometer hit its highest-ever level at 112.09 in June 2018. The reasons are many, but include changes in the corporate tax code, which stimulated spending in the industrial economy, thereby driving up demand for flatbeds, and the price of oil rallied, creating a lot of activity in fracking [for things like drill pipe and related oilfield materials].”
The other remarkable activity the industry witnessed in 2018 was the record levels of new truck and trailer orders, especially flatbeds. These orders followed the increased economic activity earlier in the year when freight rates were high and capacity was tight. According to Broughton, “orders follow price and as you can see from new flatbed order data from ACT Research, flatbed orders follow a similar path to the DAT Freight Barometer Flatbed, albeit on a three-month lag.” In 2018, new trailer orders for flatbeds (ORDERS.FLAT) peaked at close to 6,400 in September 2018 (see chart below), which represented a 54 percent year-over-year increase.

Timing is everything
At the same time carriers were placing record levels of orders for flatbeds in September, Hurricanes Michael and Florence hit the East Coast of the United States, resulting in construction activity in the Southeast falling by the most in nearly three years. This had an immediate effect on the flatbed sector, which saw capacity increase immediately with flatbed tender rejections (FTRI.USA) plummeting close to 50 percent in the second half of September 2018.
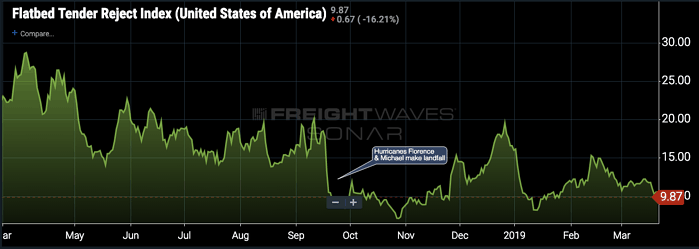
Capacity is still very loose in most markets and sectors with year-over-year outbound tender rejections in the flatbed sector down 53.62 percent to 9.87 percent, but they are still double that for dry van outbound tender rejections at 5.68 percent, which suggests flatbed operators are faring slightly better in the first quarter of this year.
Trucks aren’t where the loads are
Some of the demand for flatbeds and decrease in capacity in February can be linked to the construction boom in Las Vegas and hundreds of loads that arrive there each week, but with nothing to haul out, it makes it a year-round backhaul market (HAUL.LAS). For carriers, this means long distances between loads and a heavy reliance on load boards for the right mix of backhaul freight.
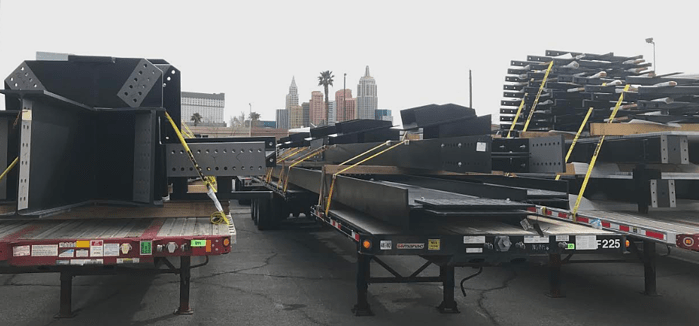
According to SONAR’s TCA Benchmarking Indices, flatbed operators have the second-longest length of haul at 665 miles (ALOHA.FCFOO) and the highest number of empty miles (EMPTY.FCFOO), averaging 16 percent of total miles over the last two years.
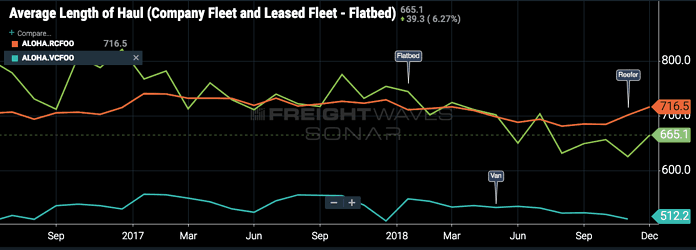
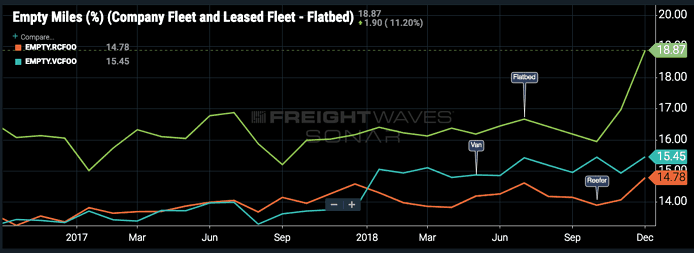
Slim pickings
The current construction boom in Las Vegas is a great example of freight flows, and to better understand the freight imbalance in this backhaul market, FreightWaves spoke to numerous owner-operators. The majority indicated that even though they can always get a straight one-drop load to Las Vegas, getting back home often means deadheading longer distances and then accepting several shorter-haul loads to keep their revenue per mile up. To do so, flatbed carriers usually either deadhead back to Los Angeles for another load, or, if heading east, “run empty 90 miles to Kingman, Arizona to load rebar from the steel mill which is usually good for 50 to 60 loads per day,” according to one veteran owner-operator. Others deadhead 400 miles further east to the heart of copper-producing country and home to the world’s largest publicly traded copper producer (Freeport-McMoRan), to load copper cathodes from anyone of a half dozen copper mines, which regionally produce around 90 flatbed loads per day.
The 2019 flatbed outlook
With record levels of Class 8 new truck orders and flatbed trailers in 2018, and delivery dates well into the summer of 2019, concerns over a slowing global economy and softening freight market makes the outlook for flatbed haulers somewhat uncertain.
While corporate tax cuts and higher oil prices helped to stimulate the industrial and energy sectors and boost demand for flatbed activity in 2018, neither of these factors is likely to provide the same boost to activity this year. Oil prices (WTI.USA) have risen in recent months, but remain below last year’s prices. As a result, fracking activity should still be generally strong but will likely not see the same growth as it experienced last year.
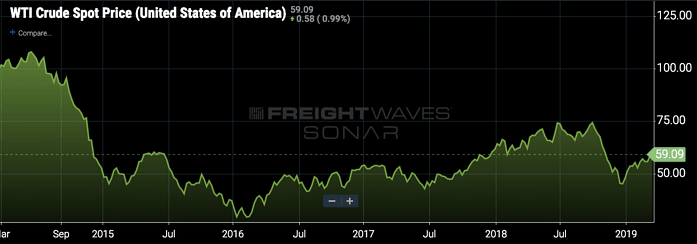
On the other hand, there is likely still some pent-up demand in construction activity, which should help things in upcoming quarters. Construction activity has yet to really recover following last year’s hurricane season, the late-2018 wildfires in California and the polar vortex in early 2019. Eventually, housing and construction should get a boost from some of this disrupted activity and should resume a gradually improving trend going forward. This should give some support to the demand for flatbeds this year and allow for some modest positive growth in activity.
The challenge is that this slight growth comes against a backdrop of expanding capacity. As the truck orders from 2018 are fulfilled this year and this capacity comes on line, flatbed carriers may well find themselves with more trucks than they need to meet the modest growth in demand. As a result, the flatbed sector should find itself far less constrained in 2019 that it was in 2018.