Port operators, users say cargo delays caused by inefficient system.
The root cause of mounting congestion problems at major U.S. container ports can be traced to low ocean shipping rates that lead to poor service trickling down through the supply chain, according to transportation service and equipment providers at a Federal Maritime Commission field hearing Wednesday in Baltimore.
Cost-cutting and efficiency programs by ocean carriers; lack of adequate investment by terminals to meet demand; and a growing driver shortage of port shuttle drivers all stem in part from a deflationary container shipping market, said representatives from the trucking, chassis, ocean liner and port industries.
Shippers put pressure on ocean carriers for low rates, carriers in turn put pressure on terminal operators to cut rates, and terminal operators can’t adequately invest in upgrades, John Atkins, the president of Global Container Terminals USA, said.
“And everyone puts pressure on the truckers,” he added.
This was the second of four meetings being convened around the country by the FMC to help drive potential industry solutions and alert Congress about infrastructure needs. Last month, the FMC held a similar hearing in Long Beach, Calif.
Many speakers said marine terminals are not adequately prepared to handle the volume of boxes dumped at once by massive new, fuel-efficient ships being deployed by carriers to slash their per-unit operating costs. In the past, smaller vessels arrived throughout the week allowing for a somewhat even cargo flow. But the bigger vessels tend to bunch up and stay longer, straining infrastructure and labor resources. The problem is compounded when ships miss scheduled arrivals because of weather or other issues. Terminals, which have a financial incentive to load and unload vessels as their first priority, have tended to neglect the container yards, causing long lines for truckers trying to deliver or pick up a load.
“A marine terminal operator’s main focus is going to be satisfying the primary business need of its customer — the ocean carrier. And today, with ships getting bigger and bigger all the time, the MTOs are focused on turning ships as quickly as possible,” Jonathan Gold, vice president of supply chain and customs policy at the National Retail Federation, said during a public comment.
“This is sensible. But it leads to business practices that are mainly focused on dockside operations. Truck gate operations are often afterthoughts. Equally important, MTOs have no business relationships with the truckers who arrive at their gates or the beneficial cargo owners that truckers haul for. Nor are MTOs rewarded by their customers for handling their gate operations efficiently,” he said.
In the Northeast and Mid-Atlantic, the ports of New York-New Jersey and Norfolk have experienced significant truck congestion.
“We did not invest heavily enough,” John Reinhart, the chief executive officer at the Virginia Port Authority, admitted. Reinhart, who assumed office in February after a long career in the liner sector, said the port has averaged 6.5-percent volume growth the past four years and is now playing catch up with process and infrastructure improvements. He said terminals have to weigh the extra expense of paying overtime to longshoremen to relieve congested yards.
Ocean carriers in recent years also have divested chassis fleets to save money, with the rest of the supply chain still struggling to coalesce around a smooth alternative system for leasing, supplying and maintaining the all-important carriage upon which containers rest.
Industry officials said shortages of chassis are common because they are not matched with the location where demand is the greatest or because they are not roadworthy due to lack of maintenance.
Many industry players favor the use of “gray pools,” where chassis are considered interoperable and can be leased to move boxes that come from any terminal or liner carrier in a port. But Keith Lovetro, the CEO and president of TRAC Intermodal, the country’s largest chassis provider, said pools need to be located outside port property because otherwise terminal operators can easily pull unionized mechanics off chassis duty to repair other types of equipment, such as refrigerated containers, or put them to work doing tasks such as snow removal.
Howard Finkel, executive vice president for COSCO Container Lines Americas and COSCO Americas Inc., said ocean carriers that still own or control chassis should get out of that business because they are providing all-inclusive rates that are being used by shippers as leverage against chassis providers to drive down rates, which is hindering the development of a healthy chassis market.
There were several calls for ports to move to truck appointment systems in response to the current practice of drivers randomly showing up — often during the same peak periods — to pick up an assigned box. Some motor carrier executives expressed opposition to the idea saying appointment systems won’t work unless someone can guarantee that trucks won’t be caught up in highway congestion. The fear is that drayage companies will lose out on business if they miss an appointment window.
Jeff Bader, president of the Association of Bi-State Motor Carriers, said no appointment system at the Port of New York-New Jersey should be tried until a system is in place to track trucks entering and leaving terminals through radio frequency identification and until infrastructure improvements in the area are made.
Ocean carrier executives, including Claudio Bozzo, the head of Mediterranean Shipping Co. (USA), said their companies are cutting back free time for shippers to make their yards more fluid, but several truckers complained that they should not be charged demurrage when a big reason they can’t pick up boxes on time is due to the inefficiency of terminals.
Motor carrier executives say independent drivers are leaving the port drayage industry in unprecedented numbers because they are so frustrated by an inefficient system that doesn’t adequately compensate them. In addition to low rates, the congestion is severely impacting their ability to make money because they can only make one or two roundtrips a day before exceeding their federally mandated limit on hours behind the wheel.
Turn times have recently increased between 5 percent and 22 percent in North America, according to Al Gebhardt, the head of liner operations for Maersk Line.
“We are using 21 percent more truckers to handle 10 percent more business because the availability is not there,” he said.
Shirley Roebuck, the president of Gilco Trucking Co., in Portsmouth, Va., said she is running 25 trucks today compared to 48 in the past because of the difficulty finding drivers. “We need shorter turn times. Then we can make five or six turns” a day, she said.
Extended gate hours, another step some ports have implemented or are considering, don’t help because drivers can’t legally take advantage under hours of service rules, she said. Advocates of extended gate hours, however, argue that truckers should adjust their work days to avoid the peak periods and use the terminals during off-peak periods.
The views of major shippers Target, Wal-Mart, Lowe’s and Johnson & Johnson were taken behind closed doors.
The NRF’s Gold called for a common set of metrics for gate efficiency because some ports measure from the time a truck reaches the gate until it exits versus the total time waiting in a queue to reach the gate.
Inadequate resources blamed for truck congestion at ports
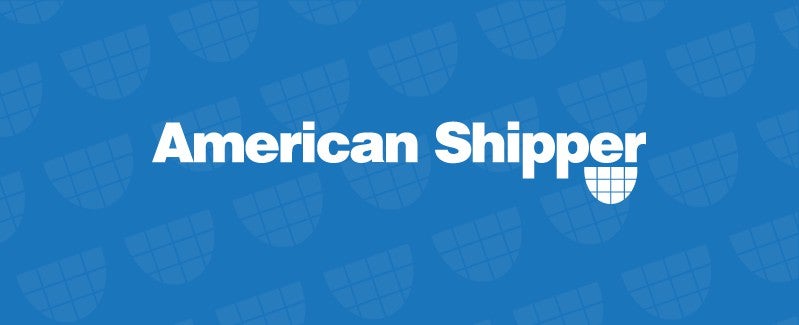