The views expressed here are solely those of the author and do not necessarily represent the views of FreightWaves or its affiliates.
In “Beat the Devil,” a film noir satire, a shady character poses a question – what is time? He answers his own question by telling his gang of thieves that time is a crook. Well, it is certainly the case that time is valuable and ought not be wasted. One of the most important constraints in logistics management is time. Limited time means that it must be rationed and allocated among only those activities that provide the highest return (i.e., net present value). Doing this properly is both an art and a science.
Just-in-time (JIT) delivery and production are attractive to companies that are able to arrange delivery of items only when needed. There are financial and physical benefits to be had when items spend less time on a company’s books and in its warehouse. Of course, there is more risk involved as well. There is an artful balance to be made in managing the trade-off between buying in bulk (i.e., in the hope of securing lower shipping costs per ton or per unit) and buying in small amounts with more frequent shipments (i.e., in the hope of lowering inventory carrying costs). Customers like it when tighter cost control translates into lower prices; but they do not like it if mistakes in scheduling lead to items being out of stock.

(Photo: Jim Allen/FreightWaves)
Uncertainty in the U.S. economy and in trade relations across the globe suggest departing from JIT in favor of building up safety stock. The feeling may be that JIT is not appropriate when there is so much flux in global supply chains at this time. It is true to say that there is never a one-size-fits-all answer in logistics management – let alone in inventory management. Therefore, some companies may still find JIT to be their best choice.
The automobile industry, though comprising less than 10% of total U.S. trade flows, is the most prominent example of JIT. U.S. exports and imports of new passenger vehicles and light trucks in 2019 totaled $59 billion and $197 billion, respectively. Volume-wise this amounted to 1.9 million vehicles exported and 8.2 million vehicles imported. For automobile parts the export and import values were $85 billion and $156 billion, respectively. About half of each of these numbers is accounted for by trade with Canada and Mexico. Certainly, the economic integration and proximity of these two countries help facilitate JIT. The United States-Mexico-Canada Agreement (USMCA) further codifies the relationship.
While the automobile industry is struggling like many other industries right now it is not likely that it will be giving up JIT any time soon. Improvements in customs documentation and customs clearance through electronic interfaces will enhance the visibility of smaller, more frequent orders. These improvements could potentially speed trade flows as long as congestion at border crossings is handled properly.
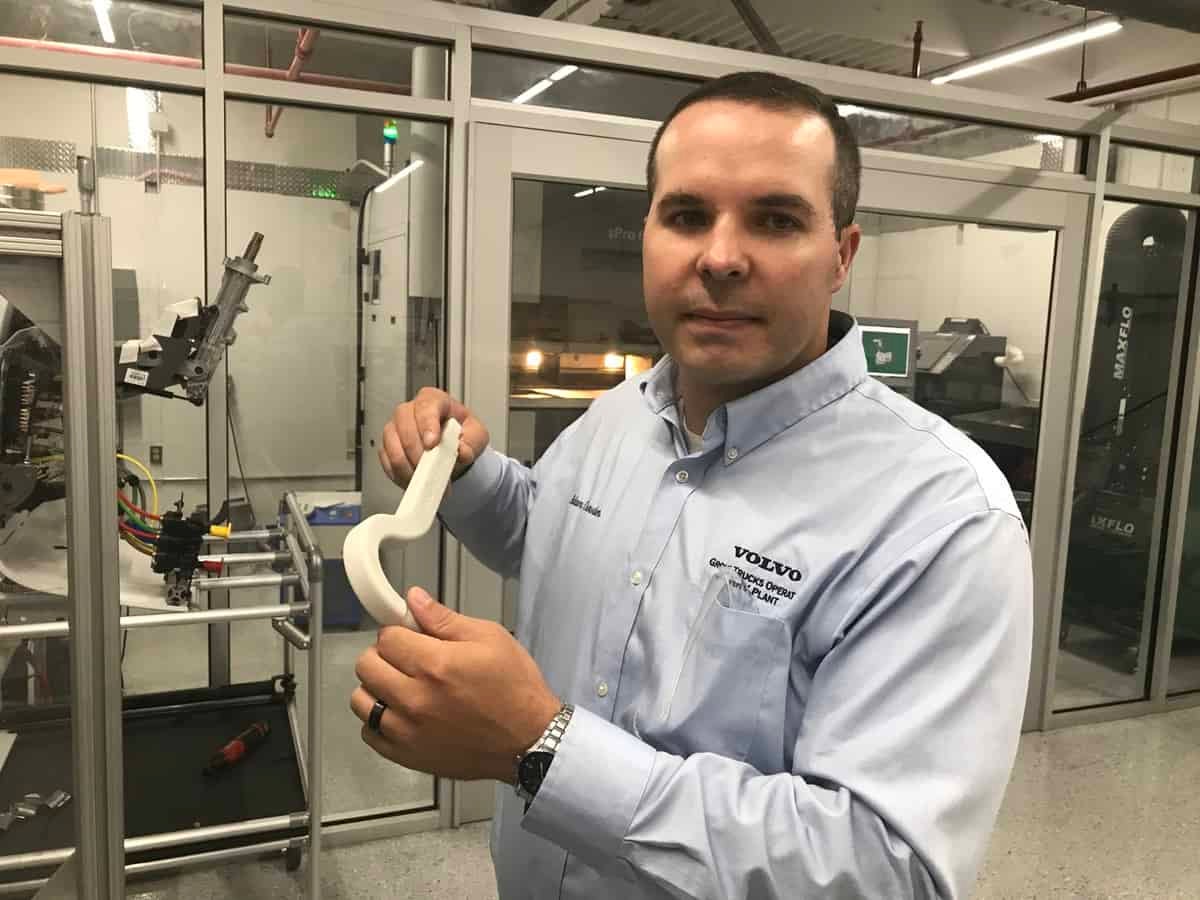
(Photo: Alan Adler/FreightWaves)
Additive manufacturing (i.e., 3D printing) applied to parts of increasing size and complexity will serve to switch the activity from JIT delivery to JIT printability. GE was an early adopter of this technology. Its Catalyst engine, used in turboprop aircraft, saw the total number of parts reduced from 855 to 12. The engine was also 100 pounds lighter. In this way, the engine requires less maintenance and is more fuel-efficient. Basically, the nature of the automobile industry is that large, expensive items such as engines can be ordered to match the scheduled daily or weekly rate of output along the assembly line.
To the extent that electric vehicles begin to displace some of the market share of those with internal combustion engines (ICEs), electric engines have fewer moving parts. This means a lower aggregate safety stock is needed. Should one of those components break or prove defective there are fewer stock keeping units (SKUs) to track. An electric vehicle essentially has the engine’s shaft as the primary moving part. Tesla’s electric engines are made up of only 17 moving parts with a single transmission, meaning no extra gears. ICEs, on the other hand, use pistons, rods, crankshafts, valves, etc. that add hundreds of moving parts per vehicle.

(Photo: Jim Allen/FreightWaves)
In the short run, the current lull in customer demand and low capacity utilization should be used by automobile manufacturers and their vendors to reconfigure their operations with an eye to social distancing and product tracking. Of course, two requirements for successful JIT programs remain the same. The first is to have excellent customer demand forecasts. The second is to have an excellent relationship with the vendor that is providing JIT fulfilment. Of course, whether it be the automobile manufacturer or the vendor that is the consignor of the JIT freight, an excellent relationship with the for-hire carrier must also be established. In this way, time constraints are dealt with collaboratively and systematically.
Click here to see other commentaries by Darren Prokop on American Shipper and FreightWaves.