The focus on the stock price gyrations of electric truck startup Nikola Corp. (NASDAQ: NKLA) overlooks a major part of its business plan — making and selling hydrogen fuel for its fuel cell trucks and anyone who wants it.
“Hydrogen is a key to everything with Nikola,” says Executive Chairman Trevor Milton. “It’s our ability to separate ourselves from our competitors. “Nikola is not just a truck company. We’re really an energy technology company.
“We’ve spent more time on reducing the cost of hydrogen than we’ve spent on anything else, including building the trucks. The trucks are just a product to consume energy, and also a product to clean up the world.”
The story surrounding Nikola’s zero-emission Class 8 fuel cell trucks is a bit confusing because the company will build a heavy-duty battery-electric cabover model before it makes more aerodynamic conventional trucks that run on hydrogen.
Production of the Nikola Tre begins next year in a German joint venture with Italian truck maker IVECO. The Tre also will be shipped in kits to Nikola’s greenfield plant in Coolidge, Arizona, where they will be assembled in late 2021 upon completion of the first phase of construction.
Beer runs for early fuel cell builds
Fuel cell truck production gets under way in 2023 when the second phase of the Coolidge plant is finished. A few fuel cell Nikola Two models will be hand-built in a pilot plant in Coolidge next year for Anheuser-Busch (NYSE: BUD), which ordered up to 800 of the fuel cell trucks in 2018.
“They’ve been a risk-sharing partner from the beginning,” Nikola CEO Mark Russell said. “So they’re going to take test trucks and accumulate miles for us and get data for us.”
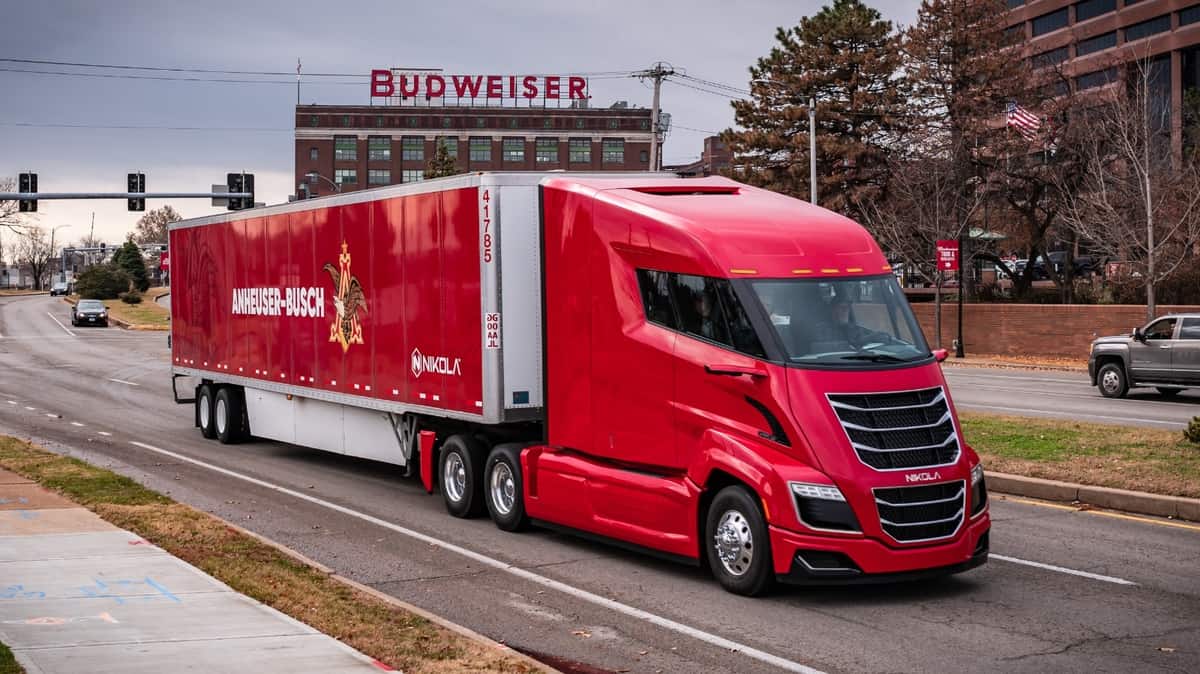
Nikola will begin building hydrogen fueling stations near Interstate 10 and close to Anheuser-Busch’s plant in Van Nuys, California. A second station is planned near a distribution center in Chandler, Arizona. The city pairing allows fueling at either end of the 400-mile route.
“We can size those stations anywhere from about 210 trucks capacity to 1,000 trucks,” Russell said. “We can fuel from 400 up to 2,000 trucks with just two stations for that city pair.”
Nikola has orders for 14,000 fuel cell trucks that it estimates will bring in $10 billion in revenue. Each truck will be leased for seven years with 1 million miles of fuel and maintenance included.
Making hydrogen while the sun shines
Nikola signed a purchase order in June for more than $30 million worth of electrolyzers from Norway’s NEL ASA. Electrolyzers use electricity to break water into hydrogen and oxygen through an electrochemical reaction that does not require external components or moving parts.
The plan is for the stations to power the electrolyzers with renewable energy from solar and wind. Both sources are unpredictable. So Nikola will operate the stations around the clock to capture energy when it’s available.
“The huge challenge as the world transitions from fossil fuels to renewable sources of electricity is [that] renewable sources do not produce on-demand,” Russell said. “That’s not what people expect when they flip switches. They expect to have electricity on-demand, but the [renewable] generating sources are interruptible and they’re variable.”
Managing the mismatch between peak availability of sunlight and wind should get easier as Nikola scales up its truck business.
“We can take a lot of that extra power at the peak and turn it into hydrogen,” Russell said. “Then we don’t have to be pulling power when the rest of the grid needs it so badly at the peak of demand.
“On the rest of the off hours, we can be taking some of that power that’s otherwise wasted right now,” he said. “We’re an answer to prayer to grid operators worldwide because we’re going to help balance these renewable energy sources into their grids.”
An expensive proposition today, but…
Most of California’s 42 operating hydrogen stations charge between $12.85 and $16 per kilogram, according to the California Fuel Cell Partnership. Those stations are designed for a small number of fuel cell passenger cars on the road like the Toyota Mirai.
“Standardization is everything when it comes to the cost of hydrogen,” Milton said. “There are almost no stations in America that use the same footprint. Every hydrogen station is built differently, has different engineering, different permits, different compressor, different everything.”
Nikola spent four years creating a common station design using zero-emission electrolyzers, Milton said.
“By standardizing it all, we’ve been able to drive that [station] cost down below $16 million,” compared with up to $50 million today, he said. The goal is $10 million per station.
“These plants are very expensive to build,” Milton said. “The reason why no one’s done it yet is because if you don’t have a guaranteed supply of hydrogen 24 hours a day you’ll never make your money back.”
Less efficient doesn’t mean more expensive
Milton acknowledges that making hydrogen to convert to electricity is less efficient than just plugging in a battery-powered truck.
“But it does not mean it’s more expensive to drive. Efficiency and cost to operate are not the same,” he said. “You can produce hydrogen very cheaply in massive amounts and sometimes distribute it even cheaper than you can buy electricity.”
In addition to fueling the trucks it leases, Nikola plans at least one public island at each station for fuel cell passenger cars. The goal is to lock in demand 18 months before a station is constructed. The goal is 90% utilization when a station comes online with at least 30 hours of storage, Nikola Chief Financial Officer Kim Brady said.
“We’re going to sell the living heck out of hydrogen to everybody,” Milton said. “Our stations are not just for us. We’re not just going to sell [it at] our location. We’re going to distribute it to others.”
Related articles:
Nikola’s first report as a public company: $86.6 million loss
Nikola pilot plant to speed electric truck production