With new intermodal yard in Decatur, ADM can move containers efficiently in the U.S. and Canada.
By Chris Dupin
Archer Daniels Midland Co., the agriculture giant that advertises itself as “supermarket to the world,” also places a high value on maintaining a reliable supply chain for its customers.
The need for transportation alternatives has been highlighted this year because of the uncertainty about whether U.S. ports will function normally with contracts under negotiation by both the International Longshoremen’s Association on the East and Gulf coasts and International Longshore and Warehouse Union Office Clerical Unit on the West Coast.
Over the past few years, ADM has greatly improved the flexibility of its supply chain and reduced costs by building a large new rail yard at a major manufacturing complex in Decatur, Ill., where the company is headquartered.
Mark Schweitzer, managing director of intermodal and container freight at ADM, said the company will supplement that later this year when it opens an intermodal terminal at the same site which will give ADM the ability to route cargo to East, West, and Gulf coast ports in the United States and Canada.
Not only will that give ADM the ability to find the best price and routing for cargo, Schweitzer said, it also gives ADM options should a port ever be shut by a strike, natural disaster or terrorist incident.
The 250-acre ADM Rail and Intermodal Logistics facility is located between two large ADM plants in Decatur. The West Plant processes soybeans while the East Plant manufactures corn products and biological products such as lysine, threonine and astaxanthin for the feed industry; and lactic acid, xanthan gum and crystalline sorbitol for food products including soft drinks, sauces and chewing gum.
When the two plants were first built, they were largely served with inbound material arriving by truck, but as they grew, rail became increasingly important for the movement of raw materials and finished products.
Prior to construction of the rail yard, the West Plant was served exclusively by the Norfolk Southern Railroad (NS), while the East Plant — which also has a coal-fired cogeneration plant — was served not only by the NS, but also the CSX and Canadian National Railway.
Not only was the West Plant captive to a single railroad, but the company had the added expense of paying switching fees if it wanted to move railcars between any of the three railroads.
In 2009-2010, ADM built its own switching yard and storage tracks for inbound trains filled with bulk commodities and coal, as well as outbound product trains.
Now the three railroads push the cars into ADM’s yard and the food company can switch cars between the three railroads without paying fees and move them at will in and out of its factories, giving it more control over its operations.
“If the corn plant is going to run out of corn at 1 p.m., and there is a corn train waiting in the ADM rail yard, the corn plant knows of this inventory on wheels and orders the material in on the most efficient run program for the plant. Then the ADM switching crew switches the train based on the plant’s schedule. No more waiting and trusting the railroad pushes the train in when it is needed,” Schweitzer explained. “Before we did not have that luxury, because you didn’t know if the train was going to show up at 4 p.m. when we were out of raw material or 6 a.m. when we didn’t have a scheduled crew ready to unload.”
Intermodal Ramp. The new intermodal facility is located at the same site, and will further increase transportation efficiencies and give ADM new options for getting product to overseas customers, Schweitzer said.
Currently, the company uses a Norfolk Southern intermodal ramp south of its plants in Decatur. With the new ADM ramp, drayage to the off-site location will be eliminated and ADM will be able to build and receive intermodal trains from any of the three railroads.
The company is building two intermodal tracks that will have a total length of 3,800 feet and be large enough to handle multiple trains each day. If future demand warrants, the company has room to add more tracks.
Weather permitting, the company expects the facility to open in mid-December. (Though Schweitzer noted that with this year’s severe drought, he would not be disappointed if heavy rains delayed the project and benefited farmers.)
The company will operate the intermodal yard through a third-party contractor, which it’s in the process of selecting.
As this issue of American Shipper went to press it was unclear whether the ILA and its employers would reach a contract agreement without a strike or lockout.
But Schweitzer said the breakdown in the talks between the ILA and employers in late August “was an eye-opener for us.”
“Having a ramp in Decatur is a prime example of why we want options to be able to arbitrage our product. If the East Coast is on strike, we can go to the West Coast. For us that is a big deal. If the East Coast and West Coast are both out, we can get our product up through the Canadian ports. We could also take cargo from Decatur to the center Gulf. We like options,” he added.
Focus On Manufacturing. The focus of the intermodal operation will be on loading containers with finished products that are used in animal feed and as food ingredients, not containerized raw agricultural goods such as soybeans, corn, or corn gluten meal.
The products manufactured in Decatur are shipped to customers all over the world. The company is also exploring possible use of the intermodal ramp for domestic shipments.
“That’s the backbone of this project, finished goods in containers that move every single day,” Schweitzer said. “If you’re a steamship line and you know you’re always going to have a load in that area, that’s an important piece of the pricing equation. Finished goods are not as variable as raw materials so it is a more steady supply chain.”
The ramp will be used to ship both dry goods in containers and liquid products using flexitanks.
By being able to build a train for any one of the three railroads, Schweitzer said ADM should be able to reduce transit times. For example, instead of getting cargo to customers in Asia by first moving containers to East Coast ports such as Norfolk that then sail back West through the Panama Canal, ADM will be able to use the CN to reach ships calling Vancouver or Prince Rupert, British Columbia, and reduce total transit time by about a dozen days.
Those regular shipments of manufactured food and feed products will make the ADM facility more attractive to railroads and shipping lines when compared to intermodal yards that move primarily raw materials, Schweitzer said.
He said some yards handling raw materials only have regular volumes of freight seasonally or only when U.S. commodity prices are competitive with producers in other countries.
ADM also plans to allow third-party shippers in Central Illinois to use the facility, and Schweitzer expects it to be popular with exporters and importers that now have to dray their cargo several hours to and from the Chicago or St. Louis ramps.
“To have an intermodal ramp that could go to the East Coast or West Coast — East Coast via the NS or CSX and West Coast via the CN — it is pretty unique,” Schweitzer said. “There aren’t many locations other than in Chicago where you can do that and even in Chicago you have a switch charge. Since we own the property there is no switch charge.”
That third-party business, as well as ADM’s regular shipments, should be a lure to both railroads and liner carriers, he said.
For example, an ocean carrier may have 400 containers located in the interior of the country that it needs to reposition overseas. Because ADM has a steady demand for containers to carry exports all over the world, if the boxes are repositioned to Decatur, ADM will be able to load those containers and give the carrier a paid movement overseas rather than having to reposition an empty box.
“ADM Transportation is continuing to move up the supply chain,” Schweitzer said. “We are working to create supply chain solutions rather than just being a ‘what’s your rate from point A to point B customer.’”
Trading Transportation. Moving grain in containers has become increasingly popular in recent years. The U.S. Department of Agriculture said more than 538,000 TEUs of grain moved in containers in 2011, 11 percent more than in the record year 2008. In the first quarter of this year, containerized grain volume was up 15 percent over the same period a year earlier.
While the focus is on manufactured products made at the Decatur plants, Schweitzer said the new intermodal yard will give ADM the ability to move raw materials by container if container freight rates are attractive.
ADM “views transportation as just another commodity,” he said, with the company using the routings and shipment method — bulk or containerized shipping — that is most advantageous.
Today, bulk shipping rates are depressed, but Schweitzer said “we’ve got to take the bad years with the good. Market economics are going to determine how and where we load bulk grain.”
For all the work the company is doing to improve its ability to move products in containers, ADM is also heavily invested in the bulk shipping business and looking for ways to improve productivity there as well.
Through its American River Transportation subsidiary, ADM has a fleet of 1,700 barges, 58 tug boats and 29 line boats. It also has a fleet of 26,100 railcars, 700 trucks, and 1,500 trailers.
Its current fleet of eight bulk vessels includes handy, handymax, supramax and panamax ships.
Last October it ordered three new 95,000-deadweight-ton dry bulk carriers that are too large to pass through the current Panama Canal locks, but which will be able to take advantage of the economies of scale the new, larger locks under construction will give to bulk shippers.
All points on the compass
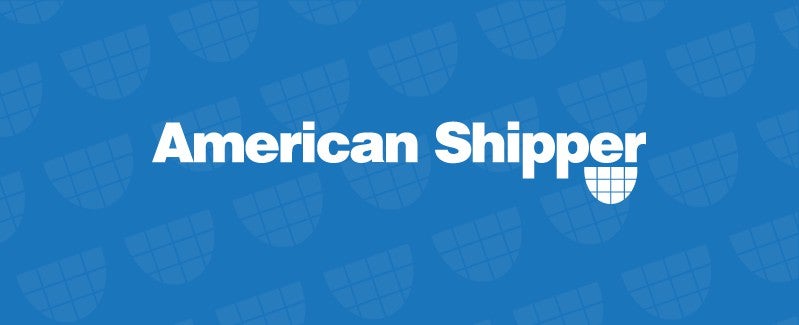